Sustainability
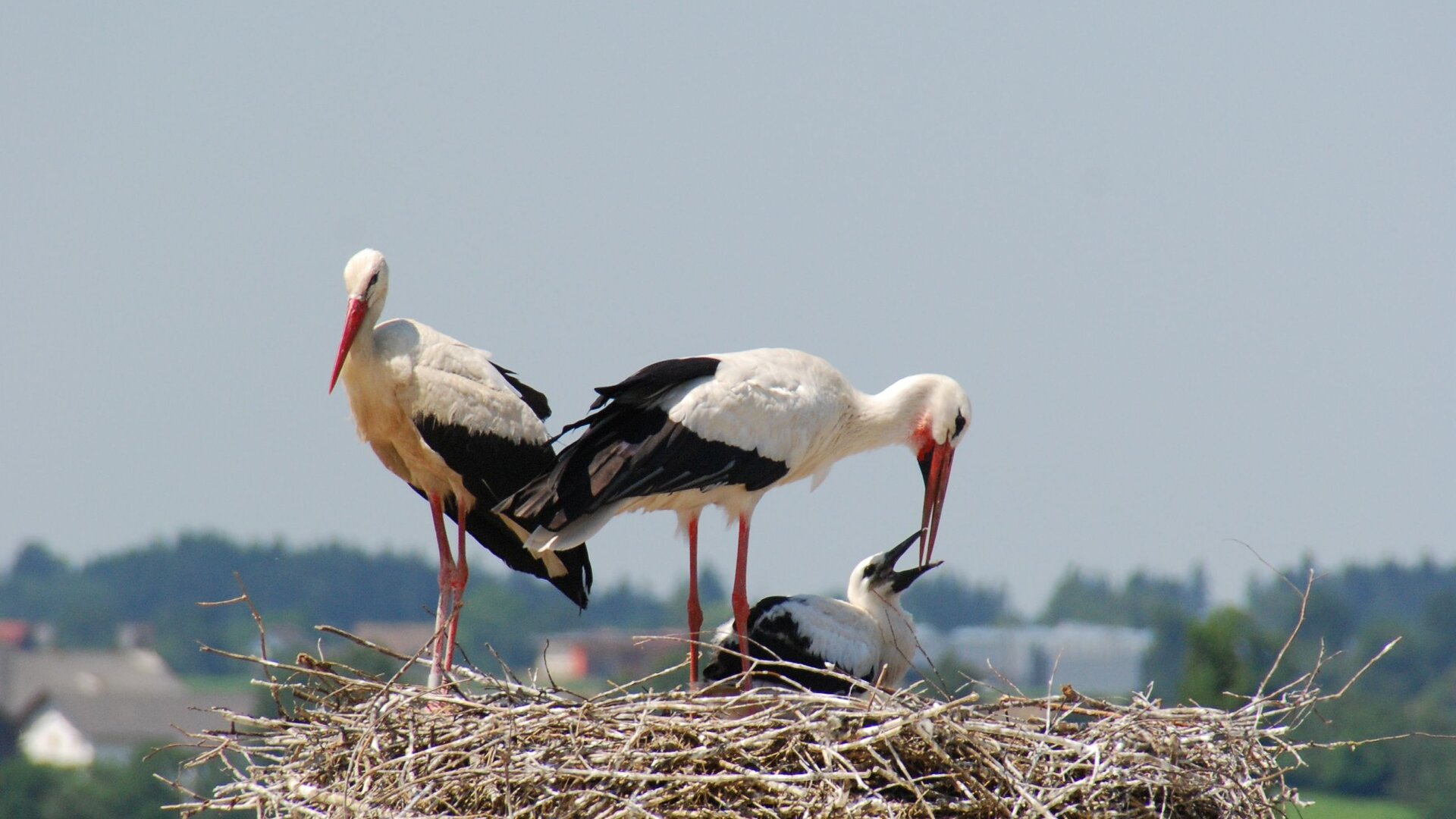
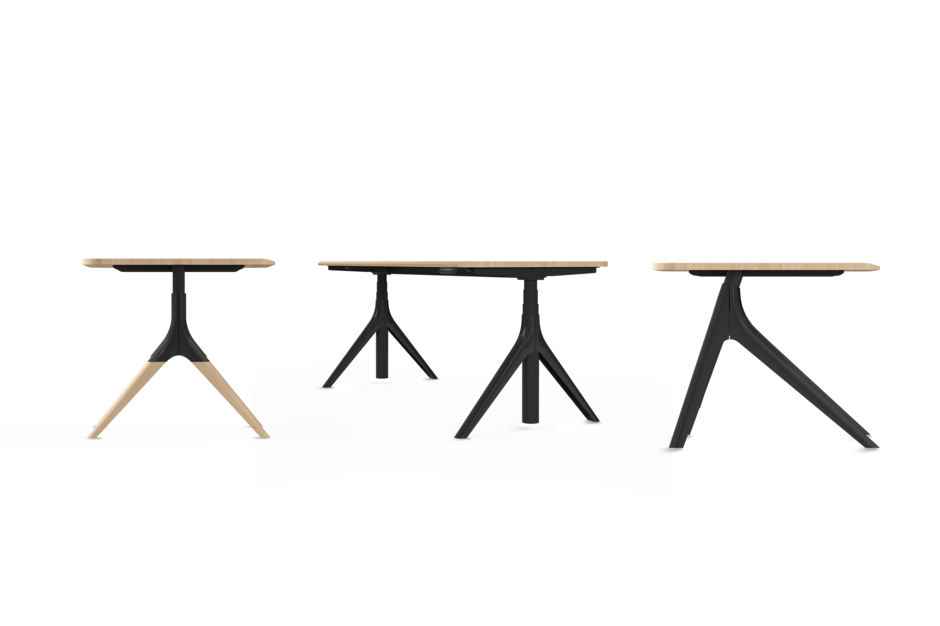
Circular Economy at Wiesner-Hager
Anyone who embraces office culture in the sense of the New Work philosophy must also adopt a forward-looking approach. This is why our goal is to radically reduce the consumption of material resources and CO2 by reconditioning furniture that has reached the end of its useful life. In keeping with circular economy, it is important to reuse as many components of a piece of furniture as possible.
Environmental impact categories
In the life cycle assessment of Wiesner-Hager, the following impact categories are analysed and shown, among others:
- Greenhouse effect (GWP) in carbon dioxide equivalents
- Ozone depletion potential of the stratospheric ozone layer (ODP) in trichlorofluoromethane equivalents
- Photo-oxidant formation and/or ozone smog formation potential (POCP) in ethylene equivalents
- Acidification potential (AP) in sulphur dioxide equivalents
- Eutrophication and/or nutrification potential (NP) in phosphate equivalents
- Abiotic depletion potential (ADP) in antimony equivalents
Environmental Product Declarations
Environmental impact
The impact assessment is based on the scientific CML process, the method of influencing factors. The following environmental consequences are analysed and shown: the greenhouse effect (GWP), the depletion potential of the stratospheric ozone layer (ODP), the summer smog creation potential (POCP), the acidification potential of soils and water bodies (AP), the nutrification potential of soils and water bodies (NP), as well as the depletion of abiotic resources (ADP).
We consider the protection of the environment as a concern of vital significance. The management of the enterprise will review these eco-political guidelines at regular intervals with regard to new requirements, and it will establish procedures required for their effective implementation into operational practice and provide the necessary means.

Sustainable Product Design
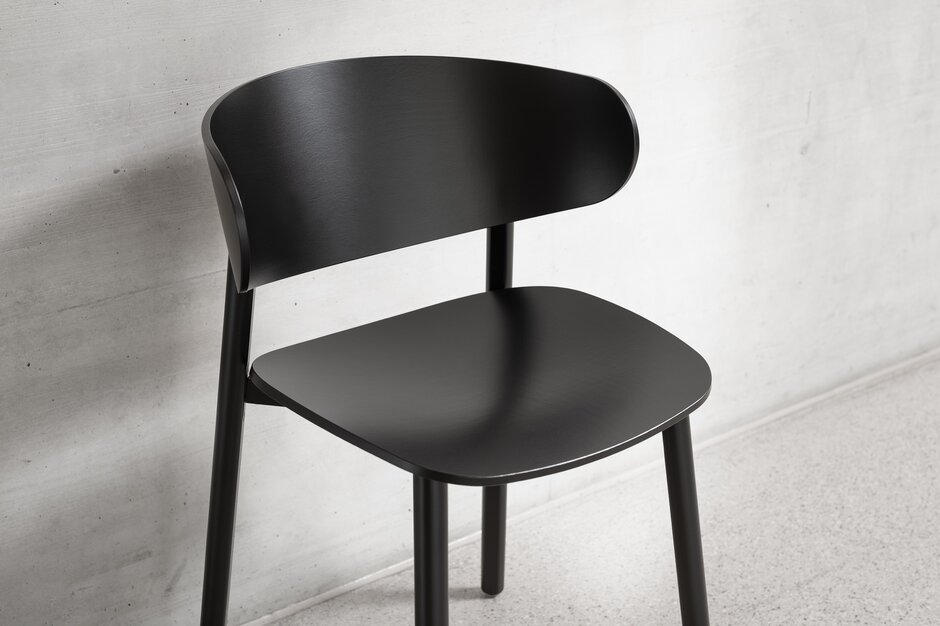
From the product specification to series maturity ecological requirements are always considered in the development process. This includes the selection of eco-friendly materials such as PEFC or FSC certified wood from forests cultivated according to sustainable forest management schemes, the use of recycled materials, or the use of more renewable primary products, to name but a few. To ensure that our products are recyclable to a great extent we largely avoid composite materials and develop dismountable constructions. Material designation, repairability and a harmonised service life of the components used are also important requirements on the product design.
Production Process
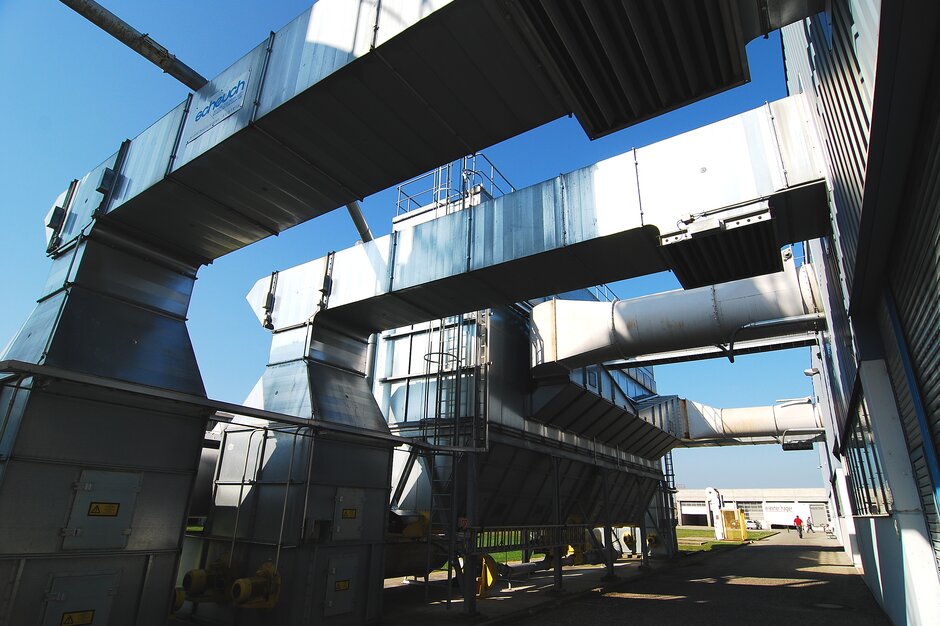
Energy-saving wood chip extraction
- Automatic adaptation to the required extraction capacity
- Lower power consumption (-30% corresponds to 80 kW)
- Lower heat demand due to 100% hot air recovery in the heating period
- Lower dust loads for employees and ambience (0.1 mg/m³)
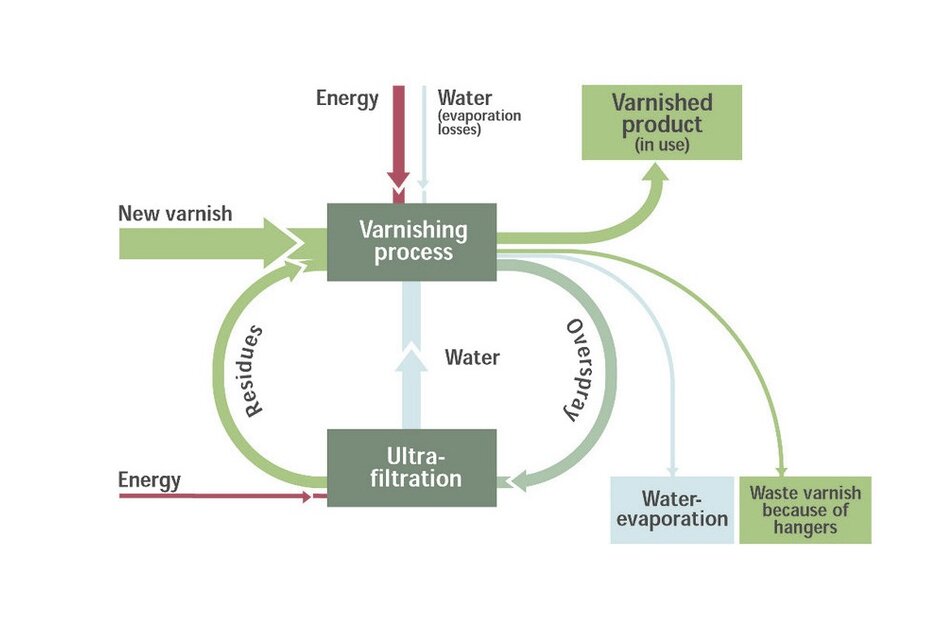
Direct recycling
The direct recycling process implemented in important parts of production made it possible to substantially cut energy and material input and simultaneously reduce waste accumulation. It is part of the extensive environmental scheme that has marked the turnaround in Wiesner-Hager's environmental policy since the late 1980s. For example, by introducing ultrafiltration of the lacquer overspray plus material recovery in wood lacquering we could save up to 70% of the lacquers and were able to slash the accumulation of paint sludge. At the same time we also introduced eco-friendly water-based paints - a significant step towards the reduction of VOC emissions. Metal surfaces are provided with emission-free powder-coating. In this case, too, almost 100% of the overspray is recovered and reused by means of state-of-the-art colour change systems.
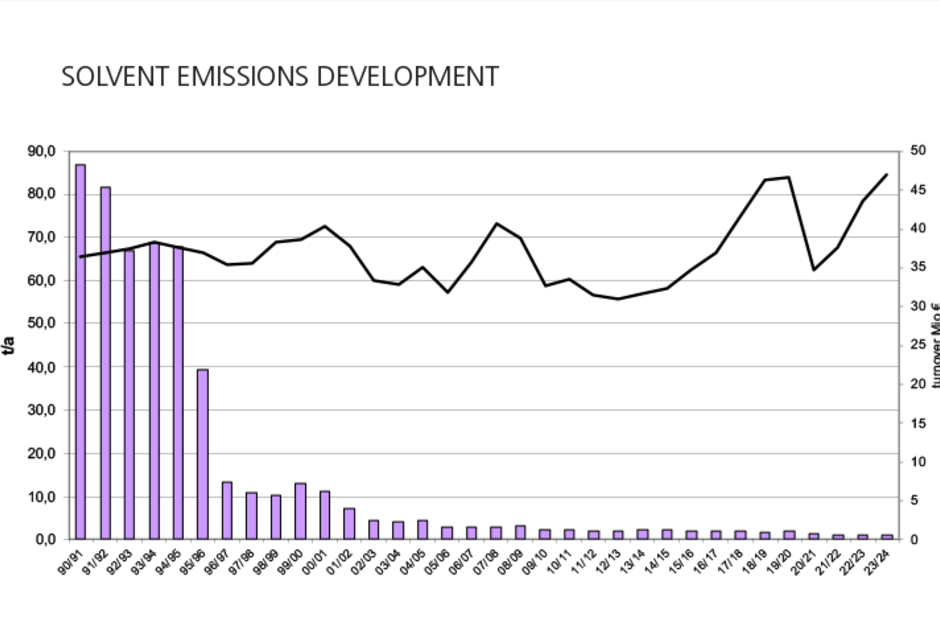
Technologies to reduce wastewater
- 3-step cascade flushing technology in metal pretreatment
- Oil separator and filter technologies for longer service lives of the treatment baths
- Modern wastewater treatment plant with automatic sampling device and measured value recording
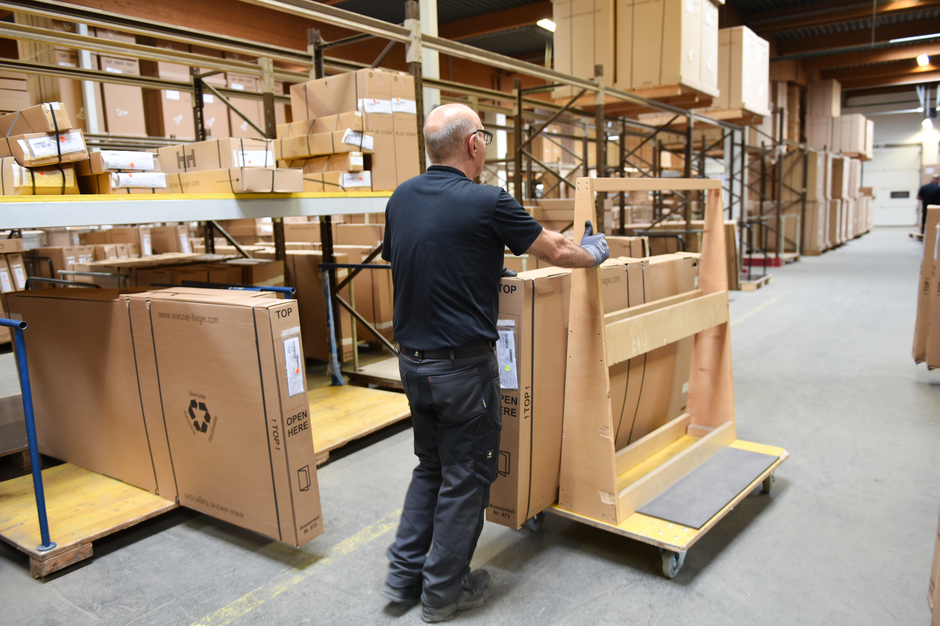
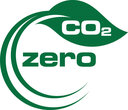
Climate-neutral waste disposal.
Sustainability begins with the packaging of our products. With the company Bonus Holsystem, we can now guarantee climate-neutral disposal of our packaging material!